What is Pre Press?
An Introduction to Prepress
Many people do not understand what Pre Press is. They are oblivious that there was and to a lesser extent now a whole industry based on pre press.
When you produce your artwork, a business card or even a magazine and send it to a printer, even if you are using an online creator, there will be somebody, at some stage, checking that artwork. It may be a person, it may be a program, but never the less your artwork is checked and proofed before sending, in the case of litho – to plate, or in the case of Digital – to print, this is the Pre Press Department. In Essence, Pre Press is the part that links design to print.
Only a couple of decades ago pre-press and reprographic departments were the lynchpin in the printing process, bringing together both design and print. 30 years ago traditional reprographics houses were the norm. Highly skilled production staff manually took artwork from the source and produced film. From the film they then produced plates for printing presses. Today most of this is now an automated process. It still needs a skilled person to spot an error even today. As with most things, many of the reprographics skills have been lost, but of course, a new set of skills have been generated.
Digital Prepress
Prepress tasks vary depending on file complexity and printing method. Flight checking now means that operator no longer have to manually check each file, The introduction of PDF virtually guarantees a perfect print job every time providing the designer has followed basic rules. But here is a brief overview of common error in supplied files a prepress operator is looking for.
- Correct size.
- Check that the file has been saved correctly.
- Examine files to anticipate and correct any common problems that could prevent the document from printing as expected.
- Double-check fonts to make sure they are embedded and will print correctly.
- Check for bleed.
- Check the job requires spot colour.
- Make sure graphics are in the right format and convert RGB files to CMYK, the format used for printing full-colour documents on a printing press.
- Trapping and knockout. Set the trapping, which is an overlap of certain colours to prevent gaps where the colours touch in a layout.
- Set the imposition of the file—putting pages in the right order for printing. It is common to print four, eight, 16 or even more pages on a single large sheet of paper that is later trimmed and sometimes folded into a single unit.
- Produce colour digital or soft proofs as requested.
Traditional prepress tasks
In the past, prepress operators produced artwork with glue and pasted artwork onto pre-printed templates before photographing camera-ready artwork using large cameras creating large bromide or film. Prepress operators made colour separations from photos, the images were split, by the camera into CMYK operations and these were individually spliced into to the film create CMYK printed images, a very time-consuming and skilled job.
Today this part of the job along with the film is no longer used. That part of the process has pretty much disappeared. Instead the whole process is computerised and the images are transferred directly to metal plates. These plates fit directly onto the press.
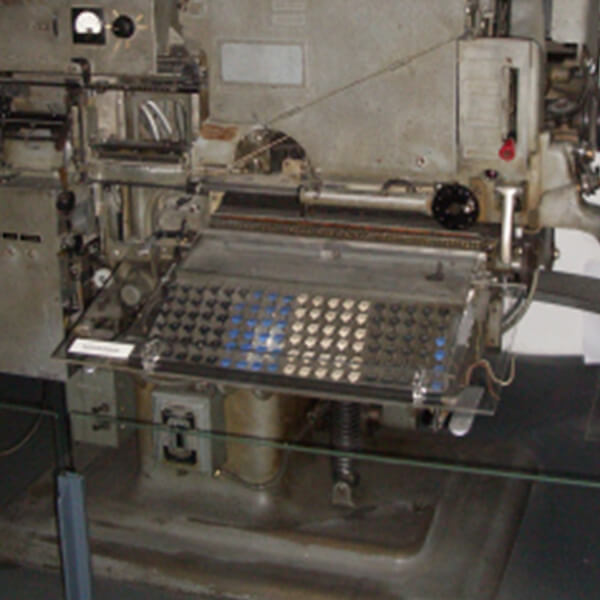
Today’s prepress qualities and requirements
Prepress operators today must be able to work with industry-standard graphic software programs including QuarkXPress and Adobe CC and Acrobat. To a lesser extent an understanding of Corel Draw, Microsoft Word and any other software that a customer may potentially use, including open-source programs. If you understand the basics well, you have a chance to find solutions when there are problems. This is, as most things are down to experience.
RipSoftware
imposition software is very complicated. It not only requires software knowledge but an understanding of how the whole reprographics and print process works. Producing a 300-page plus document to print on the B1 web press is not for the beginner. Some prepress operators are colour specialists and make subtle adjustments to client photos to enhance their appearance when printed on paper. They have a working knowledge of the printing process and binding requirements and how they affect each printing project. This knowledge is vital when producing a high-quality print. Even in a small digital print company, you will require this level of knowledge.
Did you know?
Not so many years ago typographers had to typeset thousands of characters per hour without the benefit of a screen. Yes, they typeset blind using the keyboard to generate a coded, punched paper tape. Speed was the essence, particularly in the newspaper industry because of deadlines. They also had to be highly accurate as correcting errors was laborious. There would be dozens of typographers and proofreaders setting not just editorials but advertisements as well, which were made up from tape, ink, and Lettraset all placed into a form before being photographed for plate making.
For more information: https://en.wikipedia.org/wiki/Hot_metal_typesetting